Project Overview
DROLMAA
DrolMaa is a groundbreaking inventiveness that brings a varied group of female mental health specialists together involving therapists, psychologists, healers, counselors, special educators and life coaches. This cooperative effort basically referred to as “DrolMaa Constellation,” that looks out to transform emotional, mental and psychological health by means of tailored, general ways.
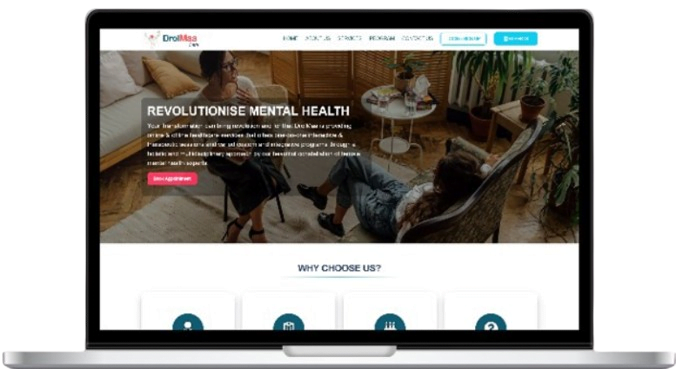
Key Features
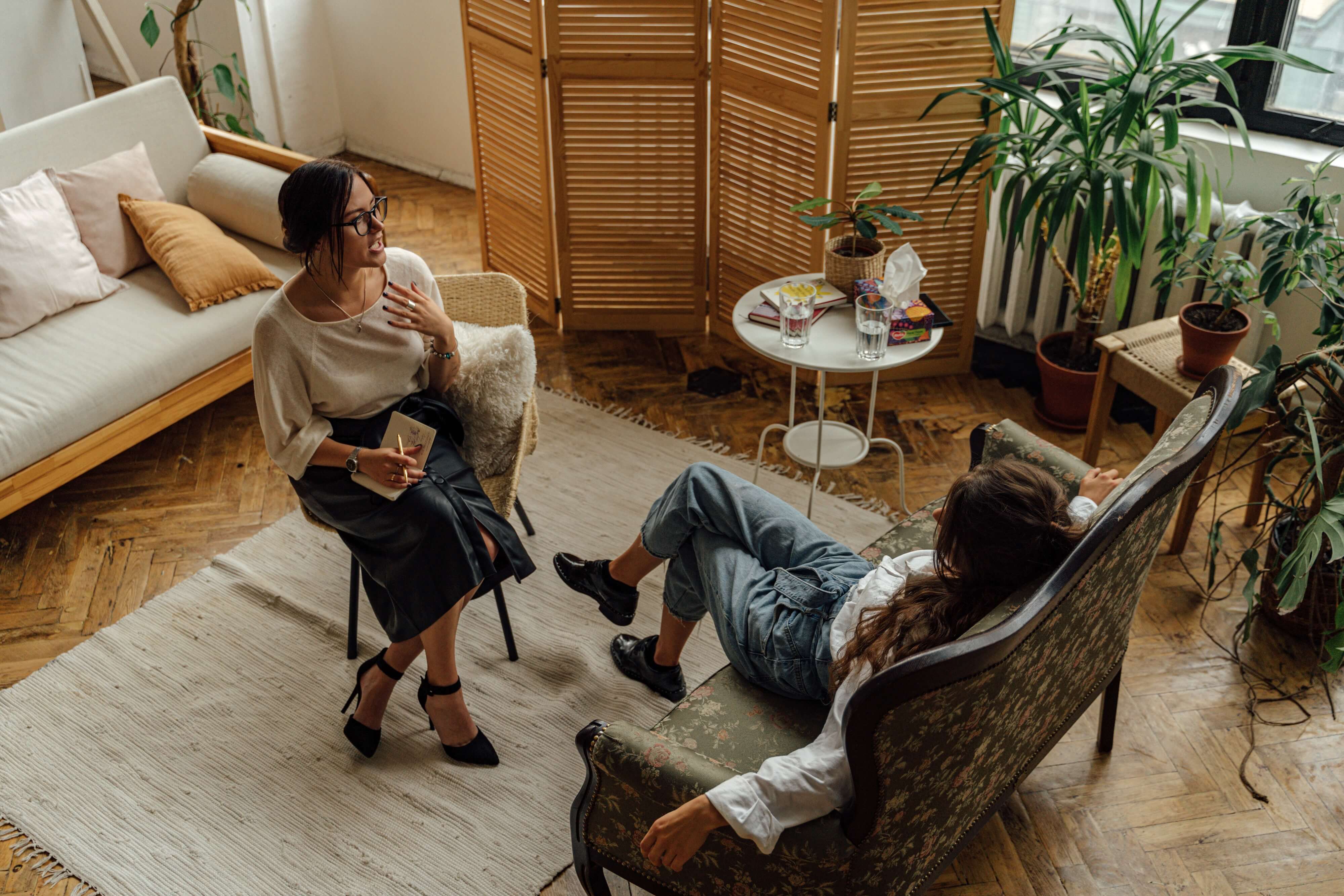
Problem Statement
ABC Corporation, a mid-sized manufacturing company, faced a significant decline in production efficiency, experiencing a 20% drop in output over the past year. This decline led to missed deadlines and increased operational costs, negatively impacting customer satisfaction and profitability. To address this issue, ABC Corporation adopted lean manufacturing principles and invested in comprehensive employee training programs. The implementation involved process mapping, waste elimination, and conducting workshops, utilizing lean manufacturing software and hiring a consultant. As a result, production efficiency increased by 30%, and operational costs were reduced by 15%. Key metrics showed a decrease in production time per unit from 10 hours to 7 hours and a reduction in defect rates.
Possible Solution
- Process Mapping: Conducting a detailed analysis of existing production processes to identify inefficiencies and areas of waste.
- Employee Training: Implementing extensive training programs to educate employees about lean principles, new technologies, and best practices.
- Technology Integration: Upgrading machinery and integrating advanced manufacturing software to streamline operations and enhance productivity.
- Continuous Improvement: Establishing a culture of continuous improvement through regular feedback sessions and performance reviews.